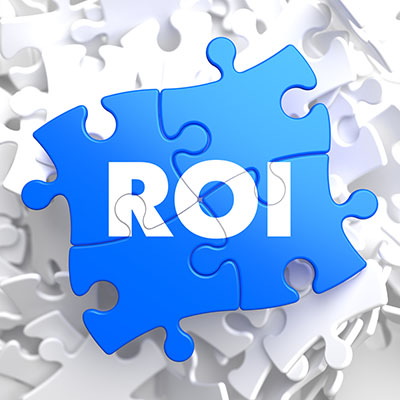
No matter what you set out to buy today, you are almost always faced with a choice—price versus quality. Whether you’re buying medical bedding, medical equipment or privacy curtains for a hospital, you have a decision to make: Do you forgo a bit of quality and save on the purchase price or do you spend a little bit more upfront and get the better quality product?
That’s why Herculite Products develops products and markets based on a strategy called —total cost of ownership (TCO). It’s a mathematical calculation that helps you determine which is the better value overall, regardless of the initial price.
Expose the Hidden Costs
If you buy a cheaper car and, between the initial outlay and the maintenance costs over the expected life of the vehicle, you end up spending more in total than you would have had you bought what seemed like the more expensive option at the time, you’ve lost in the end. Your TCO for the cheaper car means it’s no longer the most cost-effective way to go.
In a manufacturing or institutional environment, for example, when you’re considering which antimicrobial fabrics to buy, whether for medical bedding, pillow fabrics, or shower curtains, there are several other things to consider besides the initial price.
A hundred yards of imported antimicrobial fabrics with a lower price but whose antimicrobial protections don’t last more than a year or two, regardless of the life of the fabric, will always cost more in the long term, than fabrics that cost marginally more at the outset, but whose antimicrobial protections are measured and inherent in the construction of the fabric.
A Penny Saved May Be a Million Dollars Lost
Antimicrobial properties aside, don’t forget that buying medical bedding or medical curtains or medical pillow fabrics is not like grabbing a box of cereal off the shelf at the grocery store. That one purchase brings with it the cost of research to determine which product to buy, the administrative and accounting costs associated with the purchase, the materials handling charges involved in receiving and installing the materials, whether as part of a completed product or directly into service in your facility, and the cost to remove and replace the materials when they have reached the end of their lifecycle. Having to go through the purchase and installation twice instead of once in an expected life cycle can add thousands or tens of thousands of dollars to a purchase depending on the size of the facility.
So, while the more expensive purchase option is not always the better value, neither is the least expensive option always the better buy in the end, if the TCO will be higher.
To make the best decision possible, spend a few minutes writing down all the real costs involved in buying your product. These may include
- Initial cost
- Expected life of the product
- Ease and cost of getting the product serviced
- Transportation costs
- Administrative costs
- Installation costs
- Maintenance costs
- Liability exposure costs
The benefit of making purchase decisions based on the Total Cost of Ownership (TCO) is a solid bottom line. That comes from smart TCO decisions whether you’re hiring, buying, managing or marketing.